testrider
Active Member
As I had the sill panels made before I knew how much I was going to cut off I ended up with a few gaps to fill in so that I had a fairly straight line to weld to. This also meant that I could weld the jacking tube to the sill too.

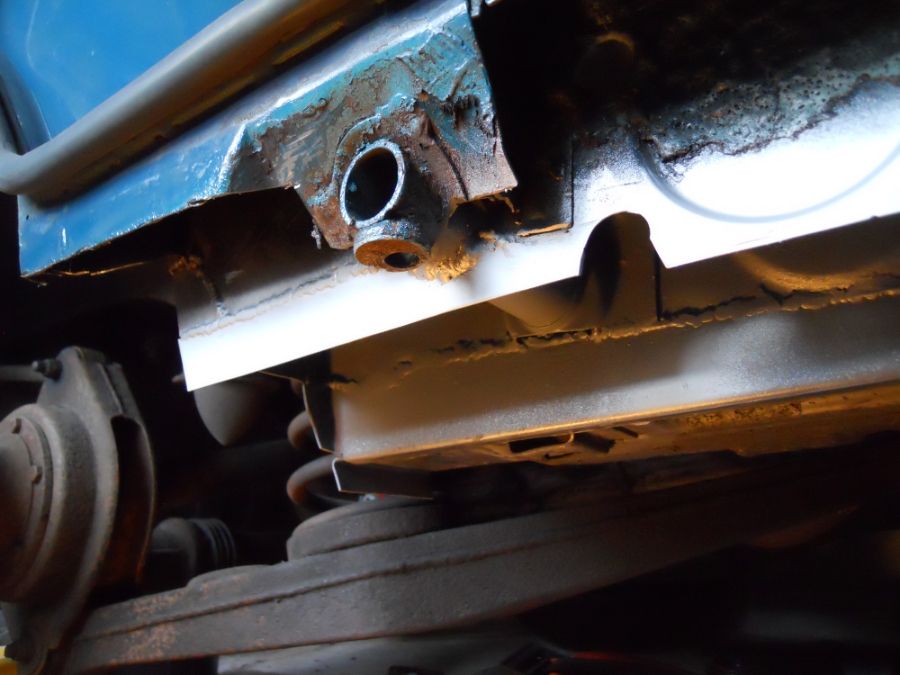
Next step was to create the spot weld flanges on the end of the sill which hold the rear wheel splash panel in place.

Trial fit and tack in place.

All welded up, I'm pretty pleased with how that's turned out.

I deliberately left the front of the sill long so that I could form the spot weld flanges in situ to get the angle and positioning right.

Everything's there for a reason.
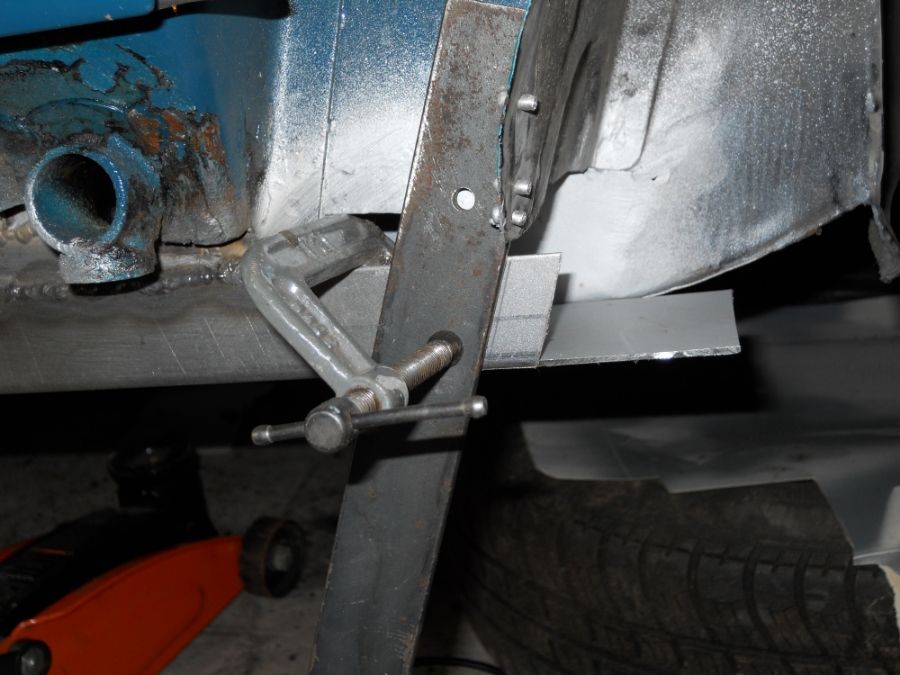

All done.

More bits to fill in at the back.


I've just got the front splash panel to make and weld in, bit of paint, refit the interior and we'll be ready to hit the road to Bowes Museum next weekend. I'll have to sort the jacking points and B post bottom when I get back. Oh, and the other side too.....

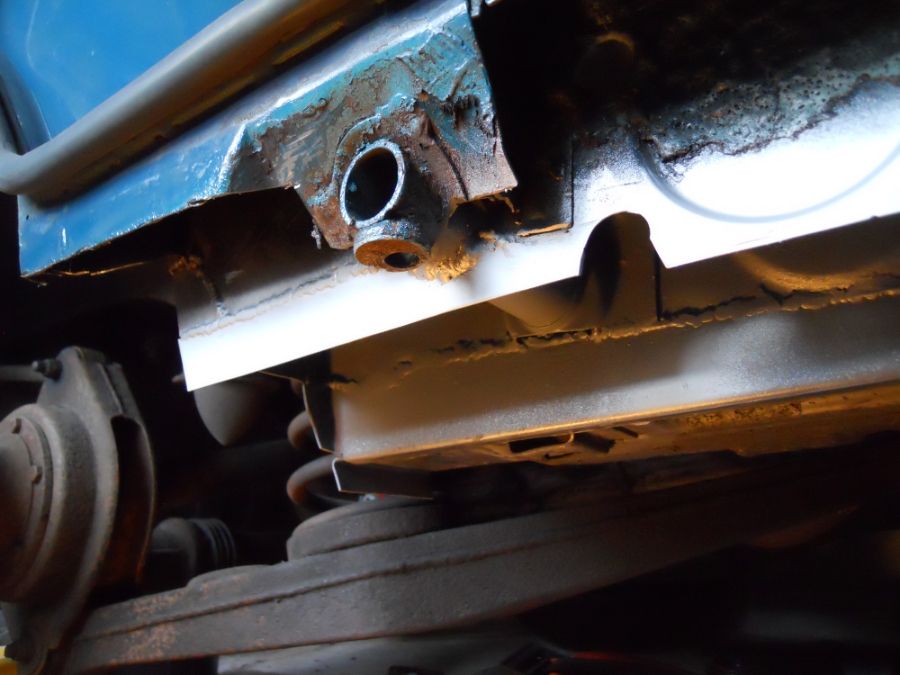
Next step was to create the spot weld flanges on the end of the sill which hold the rear wheel splash panel in place.

Trial fit and tack in place.

All welded up, I'm pretty pleased with how that's turned out.

I deliberately left the front of the sill long so that I could form the spot weld flanges in situ to get the angle and positioning right.

Everything's there for a reason.
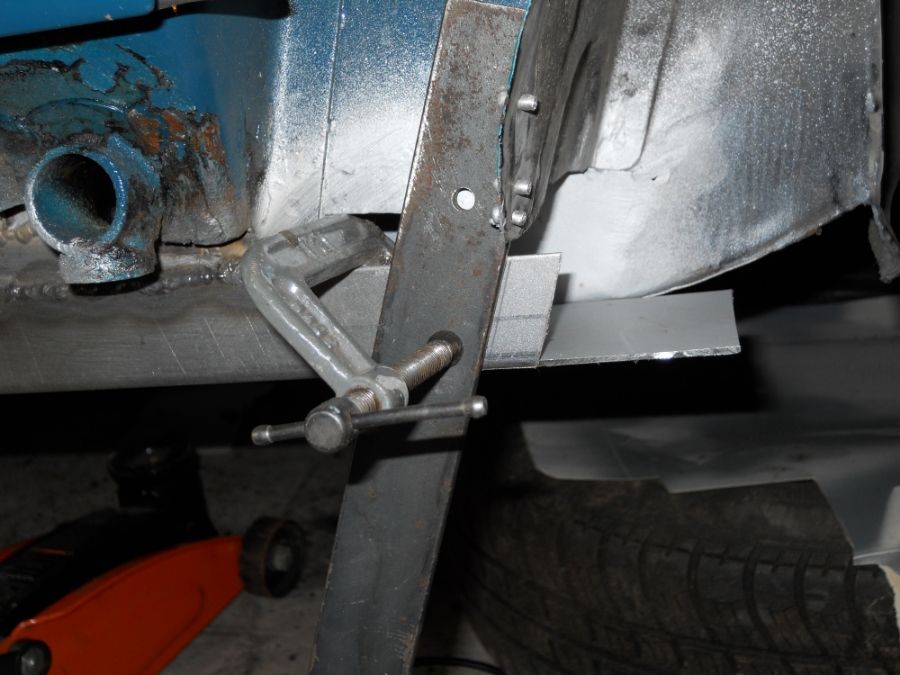

All done.

More bits to fill in at the back.


I've just got the front splash panel to make and weld in, bit of paint, refit the interior and we'll be ready to hit the road to Bowes Museum next weekend. I'll have to sort the jacking points and B post bottom when I get back. Oh, and the other side too.....