corazon
Well-Known Member
Since the last update I've fitted the second set of Outlaw calipers which have larger pistons and are in much better shape.
They needed 6mm lug spacers to centre over the vented disc perfectly. I will add some photos soon.
Diff, 3.5 engine, v8 prop, smaller piston outlaw calipers all now sold.
In other news I've begun work on my gauges idea.
I ended up buying a Corvair Monza dash pod like this
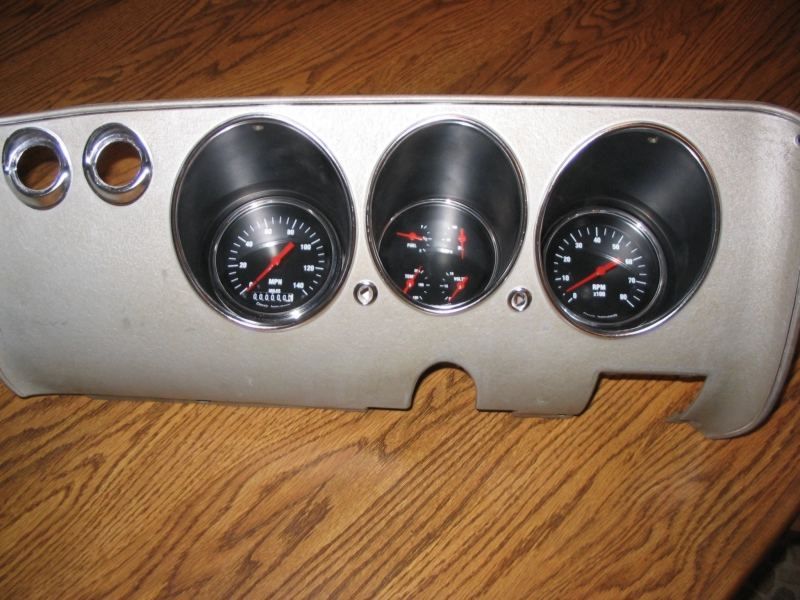
I've made the first modifications after careful consideration of whether to cut the part or the car.
A few inches trimmed off the lower edge of the corvair pod and re-bent under it now can begin to take shape in the stock gauge cluster location.
The right hand side upper edge will need trimming to follow the dashtop lines but the left will fit rather well.
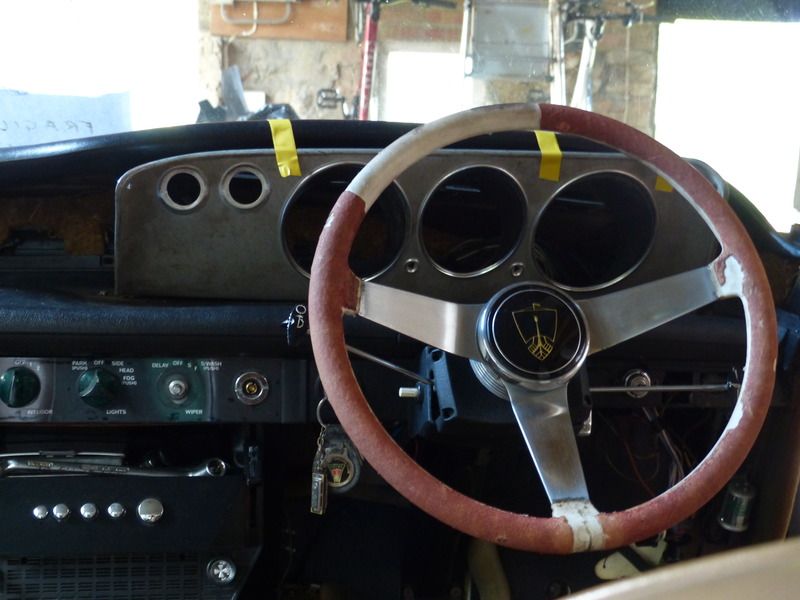
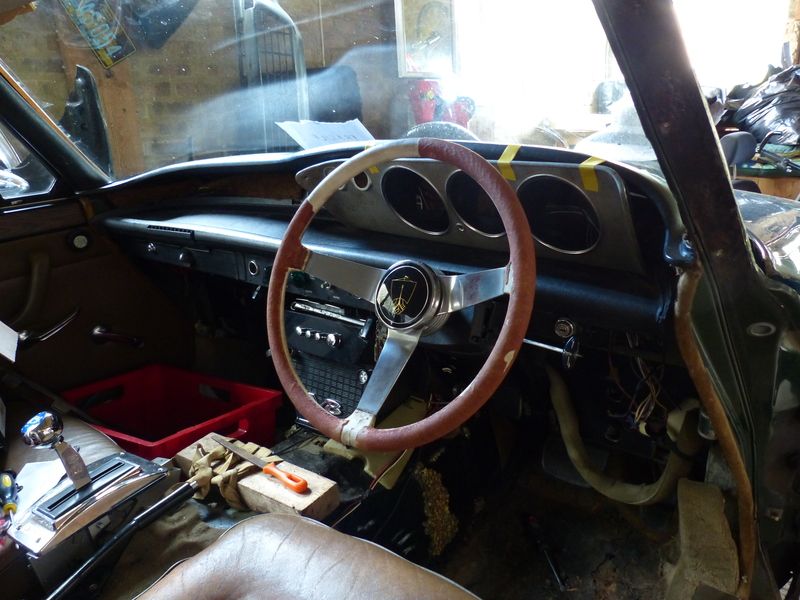
Ultimately the body of the pod will be black, and I'll re-polish the bezel rings. Something along these lines
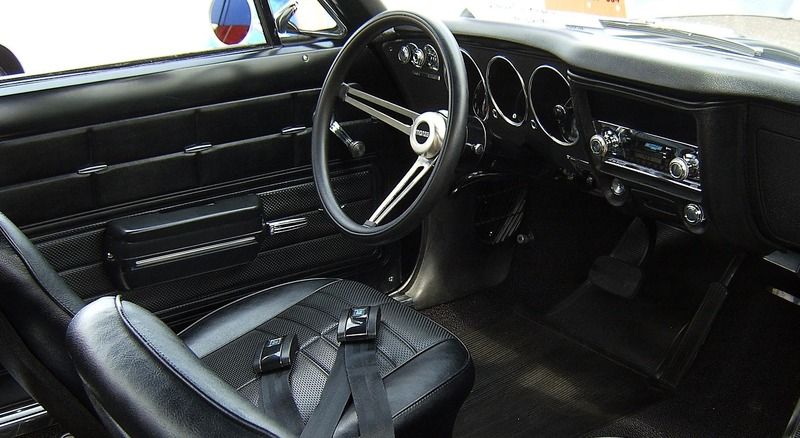
The gauges I'll be using are Veethree Black Sterling and include GPS Speedo, Tach, and 4 in 1 Fuel,Water,Voltage,Oil.
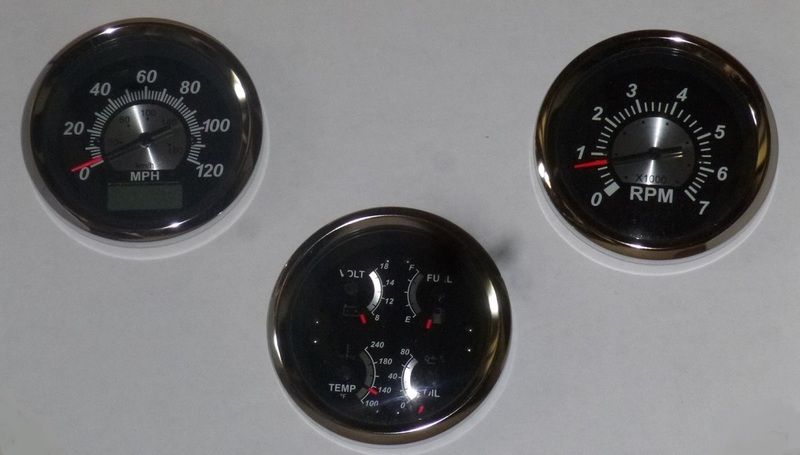
This is surprisingly one of the cheaper ways to get around the speedo issue with the ZF gearbox. Plus I'll have a different ratio at the rear end with the Jag 3.54.
The gauge set comes with GPS receiver and all other senders.
They needed 6mm lug spacers to centre over the vented disc perfectly. I will add some photos soon.
Diff, 3.5 engine, v8 prop, smaller piston outlaw calipers all now sold.
In other news I've begun work on my gauges idea.
I ended up buying a Corvair Monza dash pod like this
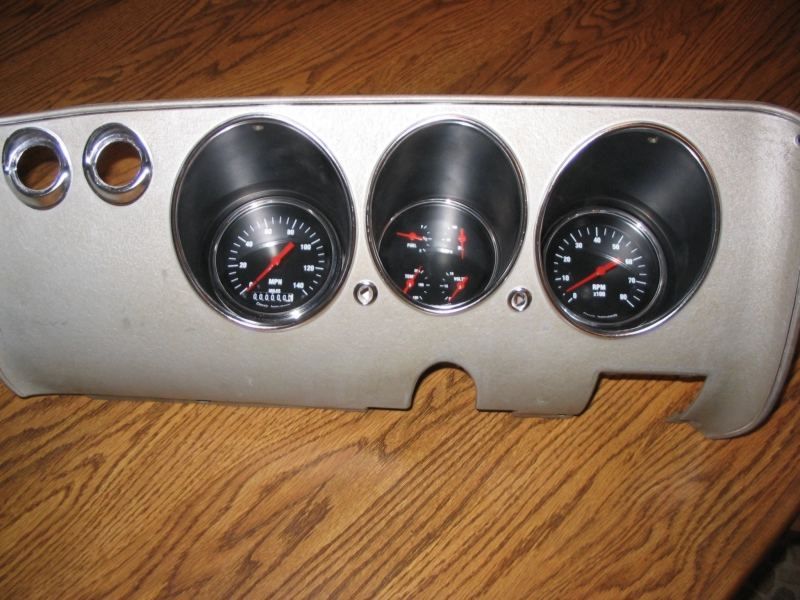
I've made the first modifications after careful consideration of whether to cut the part or the car.
A few inches trimmed off the lower edge of the corvair pod and re-bent under it now can begin to take shape in the stock gauge cluster location.
The right hand side upper edge will need trimming to follow the dashtop lines but the left will fit rather well.
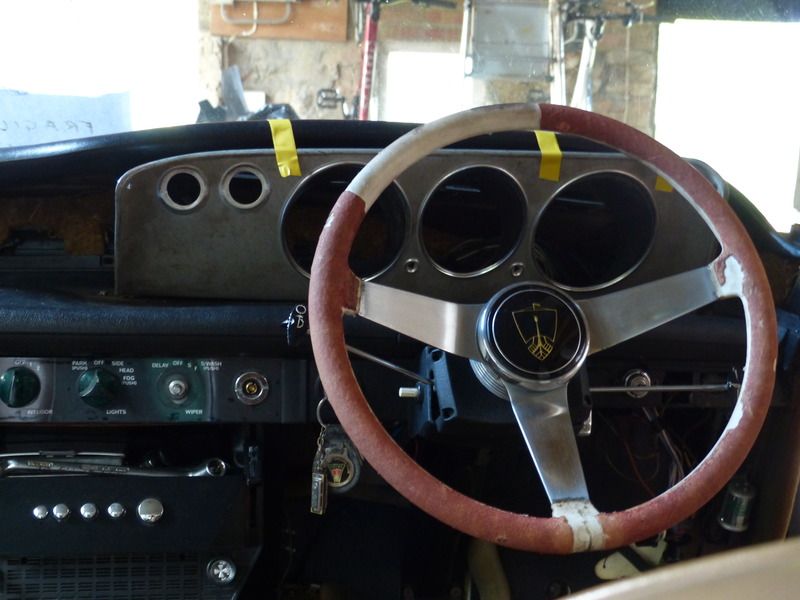
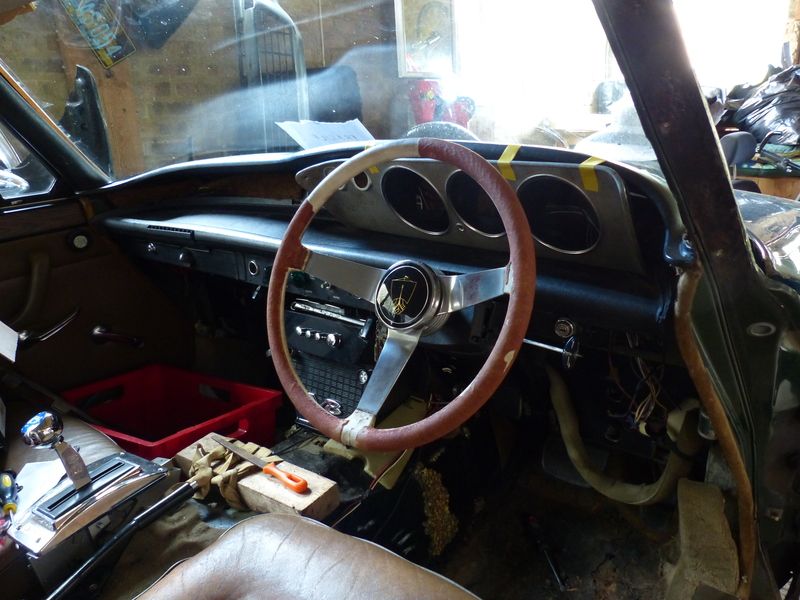
Ultimately the body of the pod will be black, and I'll re-polish the bezel rings. Something along these lines
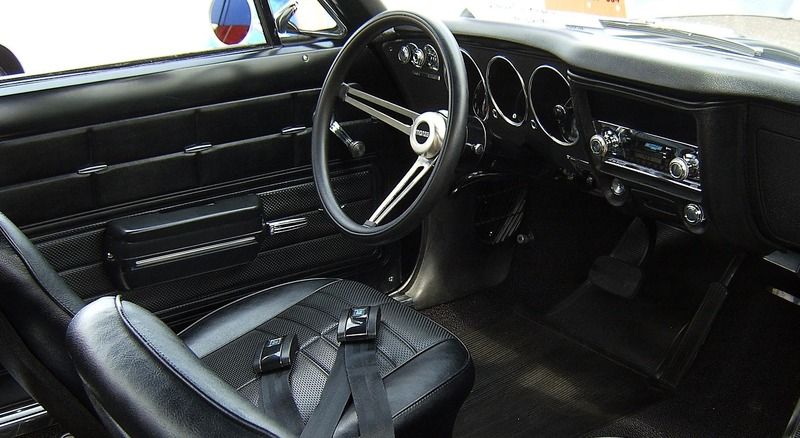
The gauges I'll be using are Veethree Black Sterling and include GPS Speedo, Tach, and 4 in 1 Fuel,Water,Voltage,Oil.
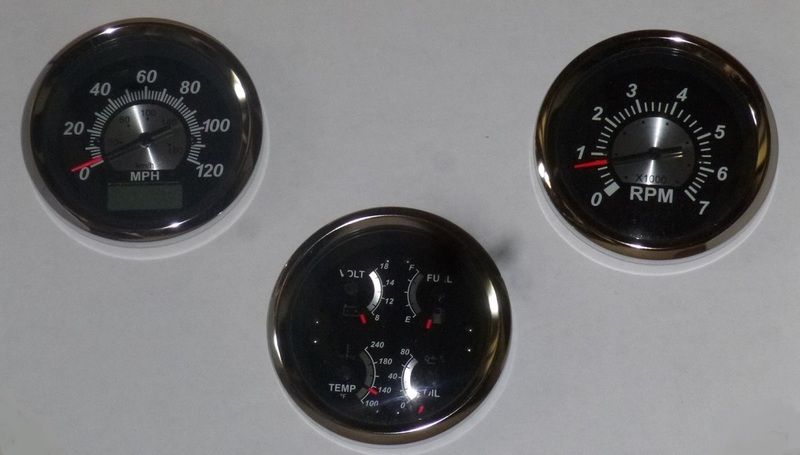
This is surprisingly one of the cheaper ways to get around the speedo issue with the ZF gearbox. Plus I'll have a different ratio at the rear end with the Jag 3.54.
The gauge set comes with GPS receiver and all other senders.